
馬達轉子測試系統專為馬達轉子線圈提供一站式電性檢測系統

可搭載移動式機櫃或是桌上型組合機規畫馬達線圈的產線設備,並且提供PC Link軟體選購,透過電腦程控與將測試數據進行存儲與報表分析,整合安規耐壓絕緣測試以及精準四線式DCR測量,此外採用脈衝高壓技術進行馬達定子線圈匝間短路測試,非破壞性的脈衝電壓利用L/C諧振原理振盪出阻尼係數之波形,透過波形差異進行比對出漆包線破皮或是線圈匝間短路瑕疵的不良品。

馬達運轉的兩大核心組件:定子線圈+轉子線圈
馬達基本結構以定子與轉子所組成,定子在空間中靜止不動,轉子由軸承支撐可繞軸轉動
定子與轉子之間有一定的空隙,以確保轉子可自由轉動,定子與轉子會繞上導電線圈,通上電流產生磁場,成為電磁鐵
轉子繞組透過集電環接到外部的電阻,調整電阻值可調整整體馬達的速度及轉矩特性
透過一個隔離的軸心將磁性材料分為幾個瓣固定環繞在此軸心四周,此磁性材料可分為硬磁或軟磁,其作用為一種導磁體,再將導電線圈一匝又一匝規律性的纏繞在磁性材料上。
馬達:槽數/極數
|
12槽(4極)、13槽(2極)、12槽(10極)
|
馬達:相數
|
單相、雙相、三相、四相、五相
|
馬達:轉向
|
內轉、外轉
|
馬達:磁性設計
|
表面貼磁、磁鐵內藏
|
馬達:繞線設計
|
分佈繞線、集中繞線
|
馬達:電流
|
直流馬達、交流馬達
|

DCR測量採用精密四線式並提供溫度補償
透過實測電阻值的分析,可初步判斷被測馬達繞組的匝數、接線方式、線徑、並繞根數以及接線質量等是否達到標準規範,繞組線圈的直流電阻要參與馬達損耗計算與溫升計算,並且直接影響馬達的性能。因此,測量DCR的檢測儀器要求精度很高,MICROTEST馬達線圈測試系統提供四線式精密測量技術與溫度補償功能,滿足馬達線圈DCR高精度測量的要求。
為什麼馬達轉子需要進行安規耐壓測試
一般馬達線圈是繞組在矽鋼片上面,避免電從繞組的漆包線導在漆包線上,因此會在矽鋼片上擺放一層絕緣材料,且漆包線材本身會附上一層絕緣漆。
為了確保生產製程中這些絕緣材料的安規品質,因此需要利用耐壓測試儀進行安規測試包含崩潰電壓、漏電流與絕緣阻抗重要檢測項目。

透過耐壓測試儀進行漏電流與絕緣測試,儀器一端接至線圈繞組,另一端接至矽鋼片,輸入一組電壓值,進行漆包線線圈與矽鋼片之間的漏電流大小以及絕緣阻值(V= iR)。
進行AC耐壓與DC耐壓測試的優點與缺點有哪些?
AC耐壓測試
大多的被測物都含有微小的雜散電容量,採用AC耐壓檢測可能無法充飽這些雜散電容,因此會產生持續性電流流過這些雜散電容。
優點
- AC耐壓貼近實際使用狀況,並可對產品進行正負極性的測試
- 因AC耐壓測試不會充飽產品自身的雜散電容,較不會有瞬間衝擊電流的產生,並且完成測試後不需對產品進行放電機制
缺點
- 遇到被測物自身帶有龐大的雜散電容或是為電容性負載,所產生的容性電流會大於實際漏電流
- 為了因應被測物自身的雜散電容所需的容性電流,儀器所輸出的電流會比DC耐壓測試時的電流大很多,對測試員的危險性會提高
DC耐壓測試
採用DC耐壓檢測會將被測物自身的微小雜散電容被充滿,因此DC 耐壓檢測所造成的容性電流,會因雜散電容被充滿後,容性電流會下降到趨近於零。
優點
- 因被測物自身的雜散電容被充滿,DC耐壓測試後只剩下實際的漏電流,故採用DC耐壓測試可明確檢視被測物實際的漏電流
- 儀器的電流容量低於AC耐壓測試時所需的電流容量
缺點
- 測試電壓必須由零開始慢慢爬升
- 當被測物自身的雜散電容量越大則DC耐壓爬升的時間越長,每次所能增加的電壓也越低,若充電電流過大時很容易造成儀器的誤判
- 完成DC耐壓測試後務必要先對被測物進行放電機制
- DC耐壓測試只能做單一極性測試

耐壓測試的時間要設置多長?
當進行耐壓測試時,測試電壓的設定會參考被測物的安全標準進行,如果設定電壓太低,絕緣材料可能會因沒有施加足夠的電壓而導致絕緣不良的產品出貨給客戶,但設定的電壓過高,量測時間太久將造成絕緣材料長久性的損害。
一般使用的時間設定參考規則,也是安全標準化會採用的方法
採用經驗值公式:試驗電壓= 電源電壓 × 2+1000V
EX:充電變壓器電源電壓為240V,則設定測試的電壓可設定為1480V
耐壓測試其實很耗時,業界生產線最常見的折衷測試方式
大多產品耐壓測試規範,持續耐壓測試時間為60秒,當單個被測物有多組數要測耐壓,則要完成一個被測物花費時間是60秒好幾倍,對產能是一種很耗時的壓力檢測項目。因此實際上生產線最常採用的方式,將耐壓測試的時間減少為1~2秒,測試的電壓提高10~20%,確保時間縮短後對產品的絕緣性能的可靠度測試。
為什麼需要進行絕緣阻抗的測試
確認絕緣體結構的絕緣性能利用優質絕緣材料組成絕緣體結構或系統,應具備較高的絕緣電阻值對於絕緣材料必須保證開關的防觸電保護確認絕緣結構經可靠度測試(如耐熱能力、絕緣性能)絕緣阻抗對元件的重要性。
電子產品組裝之前,元件的進料檢驗項目需進行絕緣阻抗的測試,這些組件包含開關、變壓器、電阻器、電容器、電感器、PCB、導線或線材,確保絕緣性能符合安全規範。
安規測試項目中絕緣阻抗是絕緣品質的重要指標
VDE和TUV等安全規範對於某些特定的產品會要求先對產品進行絕緣阻抗的測試,通過測試以後再測試耐壓性能,原因是確保被測物進行耐壓測試時,被測物自身的絕緣體不會被耐壓破壞,絕緣阻抗是評估絕緣材料性能好壞的重要電氣項目。
進行絕緣阻抗測試的方式與耐壓測試很像,耐壓測試以漏電流大小判定,絕緣測試以電阻值為判定,通常為MΩ以上,主要是量測被測物兩個端點之間及及其與週邊連接一起的各項關聯網絡所形成的等效電阻值。
電弧偵測可以確保產品發生放電不良
絕緣材料的內部或表面會因高電壓測試的狀態下產生電氣特性的放電,原因是絕緣材料已失去原先好的絕緣性能,導致被測物出現暫時性或非連續性放電。
也因為暫時性的放電無法以漏電流判定檢測不良,因此耐壓測試儀以測試電壓或漏電流之變化率進行判定出不良品。
電弧偵測是一種幾何狀非一個常量的測試,並且會因為檢測器之間線路的阻抗或分布電容導致電弧所偵測的電流對時間的變化率受到影響。
漏電流測試
利用AC電壓與DC電壓對被測產品施加高電壓下,被測物所產生的漏電流與標準規範值進行比較。
因被測物具備有一定微量的電容性存在(雜散電容),這個電容性除了會因有一定的電阻而產生漏電流,在AC電壓下,電容自身屬於一個阻抗器件,可能造成量測出的漏電流值也包含耐壓測試儀本身的漏電流值,若遇到被測物產品為低AC漏電流必須考量電容值、頻率、施加的電壓大小。
漏電流與洩漏電流大不同
是指偵測流過被測產品絕緣系統之漏電流,以高於工作電壓以上的高壓施加於絕緣系統,在被測物無工作電源之下所量測之漏電流。
是指在被測產品於工作狀態下,以最不利的的測試條件(頻率/電壓),進行被測物量漏電流,在被測物於正常工作電源之下所量測之漏電流。
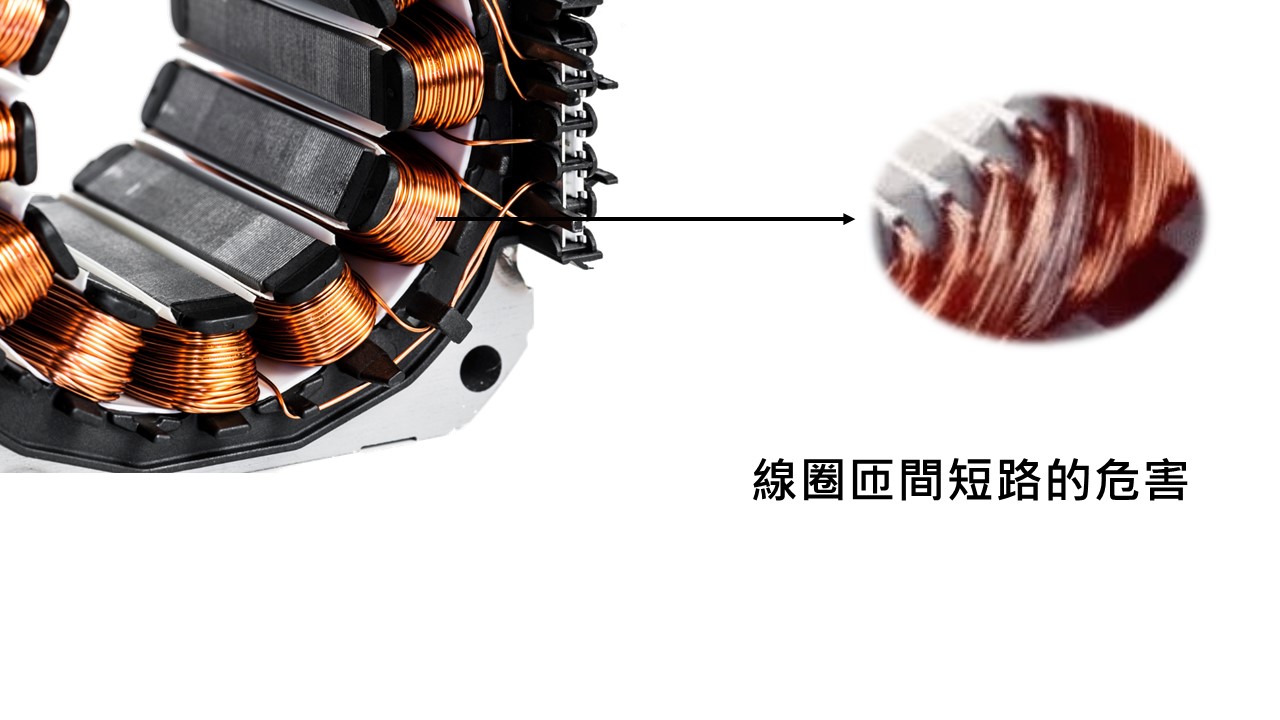
認識線圈匝間短路的問題
指的是磁性元件同一個繞組是由很多匝線繞製而成,如果絕緣不好將造成疊加在一起的線圈之間會短路,簡單而言即是此組繞組有一部份線圈直接被短路無法發揮電感作用,磁場就會和之前不同,不對稱,也將會對剩餘的線圈電流變大,若發生在馬達的運行中,振動變大、電流增大、出力相對減小。
若漆包線材有瑕疵,電流行經可能縮短路徑,產生跳電短路狀況嚴重瑕疵下可能造成燒毀
- 例如原本有50圈的路徑,可能變少為20圈
- 電阻降低造成更大電流流入,增加導通銅損而發繞燒毀
為什麼會有匝間短路的存在
漆包線上絕緣漆過程,可能刮傷漆包線,或是漆包線龜裂/氣泡縫隙
勾線/脫序/包線/繞線跨槽/附著到錫垢
匝間短路問題對馬達帶來哪些危害
發燙/燒毀:被短路的線圈將流過很大的環流 (是正常環流的2~10倍)
產生雜音:匝間短路的線圈在工作運行中振動很大
轉矩降低:被短路的線圈將電流不平衡導致轉矩降低
負載無法啟動:短路嚴重的線圈將導致電機無法帶動負載
檢測繞組線圈匝間短路的量測技術是利用『脈衝電壓與波形比對』
此脈衝電壓屬非破壞性/瞬間電壓施加於繞組線圈的兩端,在不破壞被測物繞組線圈的條件下檢測其電氣特性,透過標準品質的標準品線圈與被測物線圈比較『瞬間波形』進行品質判定。
瞬間波形:指的是線圈內部發生的阻尼衰減振盪波形

L |
為被測線圈 |
C1、C2 |
儀器內的諧振電容 |
R1、R2、R3 |
為儀器與被測物之電阻 |
量測技術 |
1.測試時首先將C1電容充電至要測試電壓
2.再以脈衝觸發SCR
3.則待測體將與C1、C2產生諧振現象
|
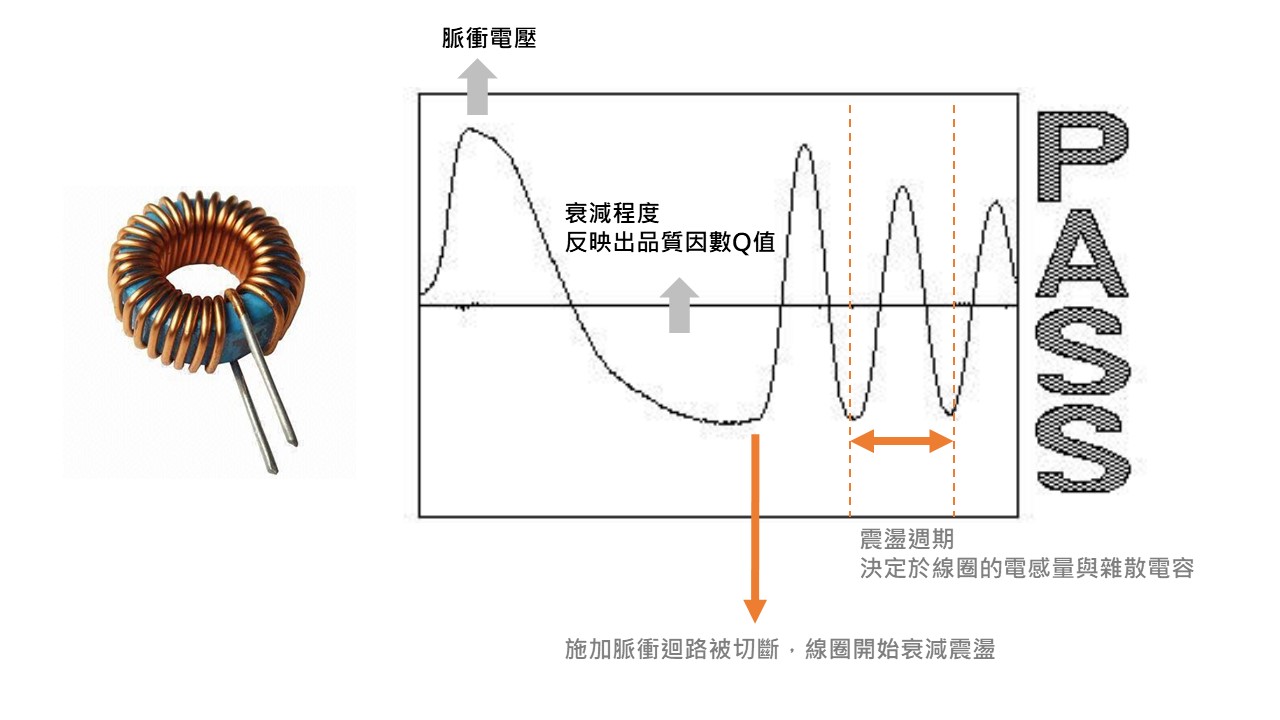
存在匝間短路瑕疵的不良品促使其波形與標準品差異不同,其波形差異反應出不良品的電氣特性已改變
- 改變的電氣特性如下
- 線圈的電感量
- 品質因數Q值
- 線圈的圈數差(電壓差)
- 磁芯的材質差異性
- 線圈內部有匝間短路

提供5種比對模式
總面積比對 |
將諧振波所涵蓋之所有面積加總稱之為「總面積」。當線圈發生匝間短路時,線圈能量損耗增加,諧振阻尼係數變大,諧振振幅會變小,總面積跟著變小,比較出不良線圈的能量損耗差異。 |
面積差比對 |
將標準波與待測波之相異處加總則稱為「面積差」。當線圈發生匝間短路時,電感變小,諧振波形相位的改變,面積差隨之改變,比較出不良線圈的電感量差異。 |
波形比對 |
將標準波設定一可容許之波形範圍,此項目可同時判斷諧振波的振幅及相位,可加大匝間短路的檢出能力。 |
電暈數比對 |
馬達線圈於高壓脈衝測試中,自身絕緣系統損壞而產生尖端放電,檢視放電曲線會出現電暈的現象,此功能可統計電暈發生的次數,比對出不良線圈是否有輕微的放電現象。 |
顫抖數比對 |
當繞組線圈有發生匝間放電的現象時,波形將產生顫抖,因此儀器將波形顫抖程度量化成數值進行比對。 |